By Leah Wilkinson
Most in the Bellarmine community have probably been teaching or going to school from their homes these past few weeks. In addition to those tasks, physics professor Dr. AK Mahmood and sophomore Jordan Dowdy have been hard at work on something else: making PPE parts for medical professionals.
Mahmood said he had been recently working with Dr. Kristin Cook, associate dean of the Annsley Frazier Thornton School of Education, and Cook mentioned the possibility of using the 3D printer in the robotics lab to make the headband pieces for the COVID-19 face shields used at hospitals and other medical centers.
“Doctors and medical staff often need to get very close to the COVID-19 patients, especially when they have to insert the ventilator tube [through] the mouth, all the way down the trachea to get to the patient’s lungs,” Mahmood said.
Because of their close proximity to those who have contracted the virus, doctors and nurses need more protective equipment than only a face mask.
“So, in addition to wearing the face masks, these medical professionals need these face shields for barrier protection of the facial area and eyes when they are treating COVID-19 patients,” Mahmood said.
Cook said she was inspired to help after hearing of other local STEAM (science, technology, engineering, arts and math) educators using their 3D printers to make PPE.
“When all of this started and we had to make the decision to cancel the March 14 STEM (science, technology, engineering and math) Maker Fair, I learned about some local STEAM teachers who own 3D printers and were using them to make face shields,” Cook said. “After mentioning it to Dr. Mahmood that we might use some of our materials to help contribute and getting access to the file, Dr. Mahmood dove right in to make it happen.”
Mahmood said he immediately called Dowdy after hearing Cook’s idea. Dowdy had been working with Mahmood in the robotics lab prior to the campus closure. “So we started to work on it right away,” Mahmood said
The contamination of the face shields is a big concern in the U.S.
“Currently due to this shortage of these face shields, the healthcare professionals are often sharing the same face shields with others or reusing the same face shield to treat multiple COVID-19 patients,” Mahmood said.
Mahmood said there are three pieces needed for the face shields.
“One piece is the headband that goes across the forehead, which is what we made,” Mahmood said.
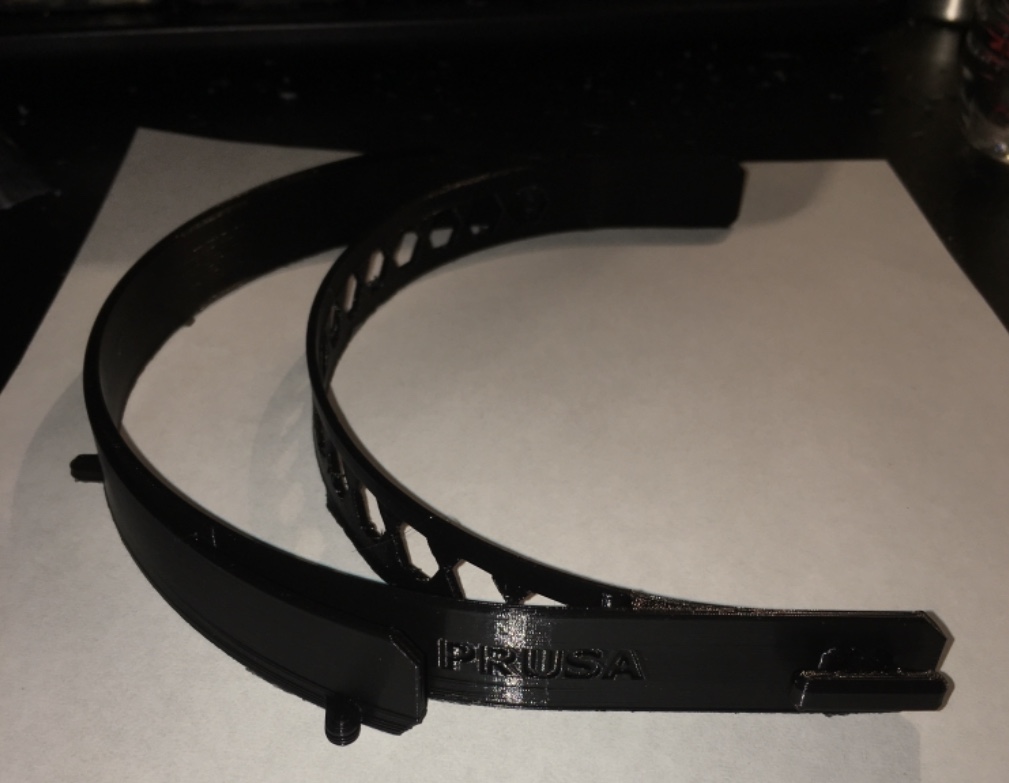
Dowdy said he had to improvise after things didn’t go as planned in the beginning stages of the project.
“Once I projected the dimensions of the COVID-19 headband frame using the 3D printer software, I noticed that the print area of the 3D printer was smaller than the actual size of the COVID-19 headband frame, so I could not use the robotics lab’s 3D printer,” Dowdy said.
Dowdy said he used his own 3D printer he had on hand.
“Fortunately, I had a 3D printer at home that I use occasionally.”
Dowdy said his printer worked perfectly.
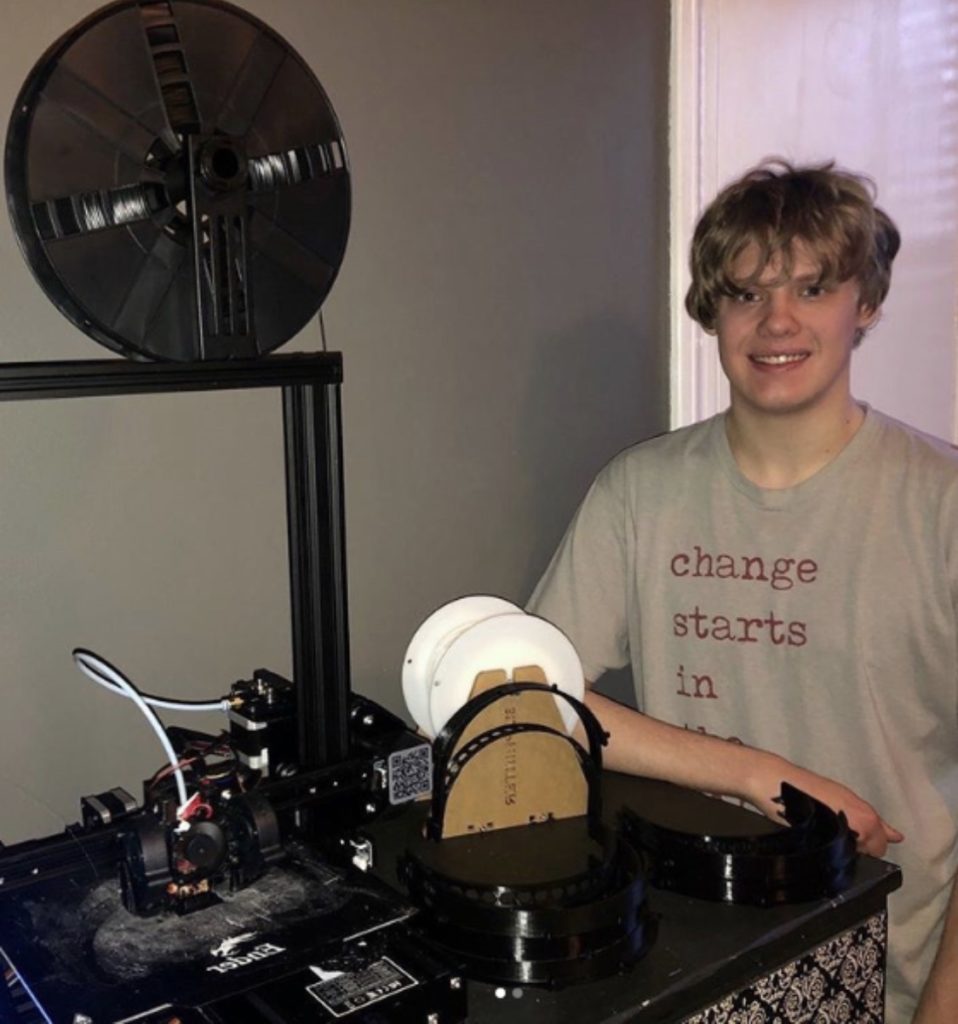
“For these face shields, we can make about five head bands (also known as face shield frames) per day with the 3D printer I am using,” Dowdy said.
Mahmood said the pieces are currently being distributed locally.
“Right now we are mostly focusing on the needs of the local healthcare professionals who are treating the COVID-19 patients at the local hospitals in Louisville,” he said.
Mahmood said he received an email from a doctor in Los Angeles who found out Mahmood and Dowdy were making the pieces.
“She mentioned that due to the nationwide shortage of these PPEs, at her hospital they are sharing the same face shields among her colleagues to treat COVID-19 patients,” Mahmood said. “So we are planning to make some 3D-printed COVID-19 headband frames for that hospital also.”
Mahmood said he’s also open to helping more medical professionals in other parts of the U.S.
“If we get requests from other hospitals, we can certainly make more of these.”
Cook, who has delivered the pieces to “one of many donation sites asking for them throughout the city,” said she admires Mahmood’s readiness to contribute to this cause.
“With all of the changes to course delivery, continuation of the grant work, and everything else that has kept everyone busy during this shift, I was super impressed with Dr. Mahmood’s dedication and willingness to do what he could to help,” Cook said.
Mahmood said he and Dowdy are planning to make other pieces soon.
“Next, we are also focusing on 3D printing splitters for ventilators,” Mahmood said. “Due to the huge shortage of ventilators, hospitals want to share one ventilator for two COVID-19 patients.”
Mahmood said the pair hope to make these new parts within the coming days.
“We have the design so that we can 3D print splitters for at least three common ventilator models,” Mahmood said. “We are planning to test these 3D printed splitters first and then if all looks good, we will start printing them sometime next week once we know how many are needed by the local hospitals in Louisville.”